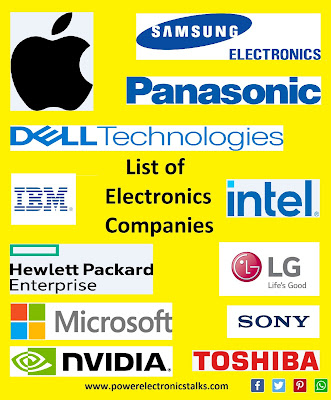
Electronics Companies
List of Electronics Companies Here is the list of some well-known electronics companies in alphabetical order. These electronics companies a...
Read More
Power Electronics, Power Factor Correction, Ferrites, Power Converters, Power Electronics Components, Power Electronics Applications, Standards and Testing, Product Review, Tools and Calculators